Väljakutse
Rahututes vetes liikumine
ArcelorMittal seisis silmitsi pettumust valmistavate logistiliste probleemidega, mis puudutasid nende terasmähiste saatmist mandrilt oma klientidele Loode-Inglismaal. Idaranniku sadamate, näiteks Port Sutton Bridge'i sadama läbilaskevõime on piiratud, kuna vesi on madal ja veoautod ei suuda terasmähiseid läände vedada.
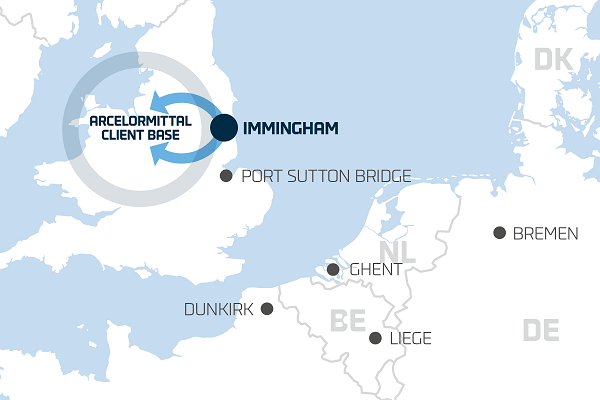
Lahendus
Üks rajatis, palju võimalusi
Probleemi lahendamiseks soovitasime ArcelorMittalil kasutada meie teraseterminali Imminghamis. See on ideaalne lahendus nende suure mahuga veovajaduste rahuldamiseks, kuna meie lai valik varasid kohapeal tagab suure paindlikkuse ja turvalise käitlemise.
Kaks 35-tonnise võimsusega magnetkraanat vähendavad mähiste kahjustamise ohtu maha- ja pealelaadimise ajal, samas kui lihtne juurdepääs raudteele ja maanteele tagab probleemideta edasise veo.
Imminghami terminal mahutab kuni 20 000-tonniseid laevu – tunduvalt rohkem kui väiksemates idaranniku sadamates. Sellel on ka 100-tonnise võimsusega sadamakraanad, köetav ladu ja suurte kogemustega meeskond, kes on seitse päeva nädalas saadaval, et ArcelorMittalit vajadusel abistada.
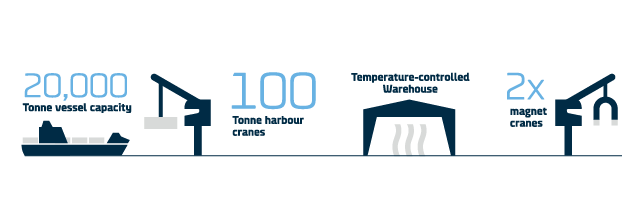
Sujuv, koordineeritud protsess
See toimib järgmiselt: me korraldame ArcelorMittali terasmähiste saatmise sadamasse ja liigutame need lattu või otse meie maantee- ja raudteevarustusse vastavalt vajadusele 24/48 tunni jooksul. Me lähetame 4-5 rongi nädalas, millest igaüks veab kuni 1200 tonni terasmähiseid 10-12 vagunis. Lisaks sellele on meil Imminghamis maanteevõimsus, et transportida mähismaterjali veoautodega, millel on haagised.
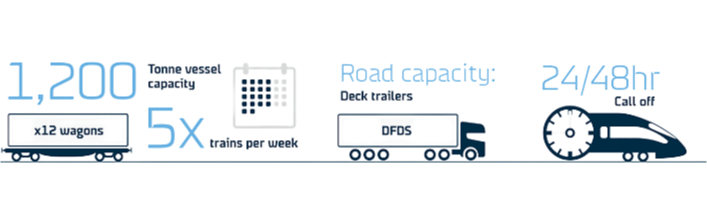
Tulemused
Suuremad mahud, väiksem risk
ArcelorMittal on alates Imminghami teraseterminali kasutamisest oma mahtu pidevalt suurendanud. Üheks oluliseks eeliseks ettevõtte jaoks on terminali magnetkraanad, mis vähendavad mähiste kahjustamise ohtu.
„Tänu sellele, et kasutasime mähiste käitlemiseks oma laos magnetkraanat, on meil väga madal mähiste kahjustamise määr. Autotööstuse nõudmiste tõttu on meil mähiste kahjustamise suhtes nulltolerants, seega on väga oluline, mitte ainult ArcelorMittali, vaid kogu tarneahela seisukohast, et säilitada selline madal kahjustamise määr.“
- Ian Penistone, tegevdirektor, DFDS