Challenge
Meeting changing customer – and company – needs
Changing customer needs and ventures into new business segments meant Holmen needed to adapt its logistics solution.
The company’s mills in Braviken and Hallsta produce paper for magazines, books, and newspapers for the Swedish and other European markets. Both mills are located on Sweden’s east coast, which meant Holmen would ship its products in bulk every week. From warehouses in Terneuzen, NL, Sheerness, UK and Lübeck, DE, the products would then be distributed to customers via call-offs.
Large volume handling
Over time, more of Holmen's customers began requesting 'just in time' delivery, meaning smaller orders and shorter lead times. Additionally, customers were increasingly shifting production between various European facilities. This required a logistics solution capable of handling large volumes from the mills, while also offering the flexibility to adapt to changing capacities, markets, and customer needs.
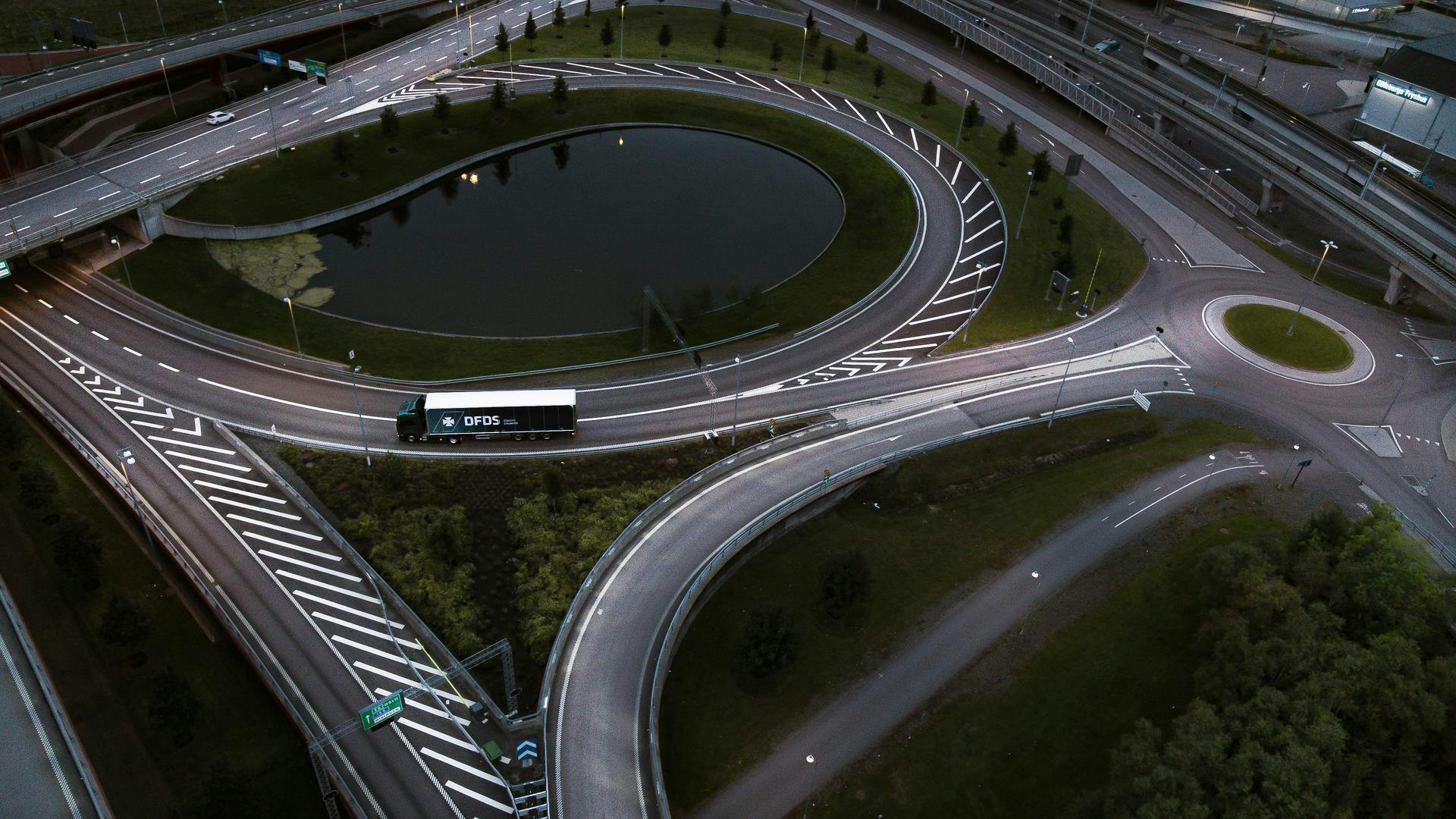
Solution
An intermodal transport solution
Here's how we helped Holmen solve their challenge. First, we collaborated closely with them to evaluate their existing logistics solution for shipping products from their Swedish mills. Our analysis showed that Holmen could benefit from DFDS's logistics network. By adopting an intermodal solution—combining sea, road, and rail transport—the company could move its products with greater flexibility, efficiency, and sustainability.
New routes to three markets
The new routes we developed began by shipping Holmen’s products by train and truck from the mills to Gothenburg. They were then moved onwards on DFDS ferry routes to Immingham, Ghent or Zeebrugge and then directly onto their customers in those markets. We subsequently developed more intermodal solutions for their transport routes to meet new customer demands.
Results
The new end-to-end supply chain solution minimises risk and is scalable to changing needs. Access to real-time transport data optimises Holmen’s logistics network, and the new system’s flexibility and efficiency save time and reduce costs.
“The sustainability aspect of the intermodal route between Rosersberg and Gothenburg was very attractive, as was the frequency of departures from Gothenburg to the UK and Continent. Working with DFDS was a great opportunity, as it allowed us to secure the large and flexible capacity we needed.”
- Ronny Björklund, Senior Logistics Purchasing Manager, Holmen